Tech stack in small and midsize factories
- 09 Jul, 2024
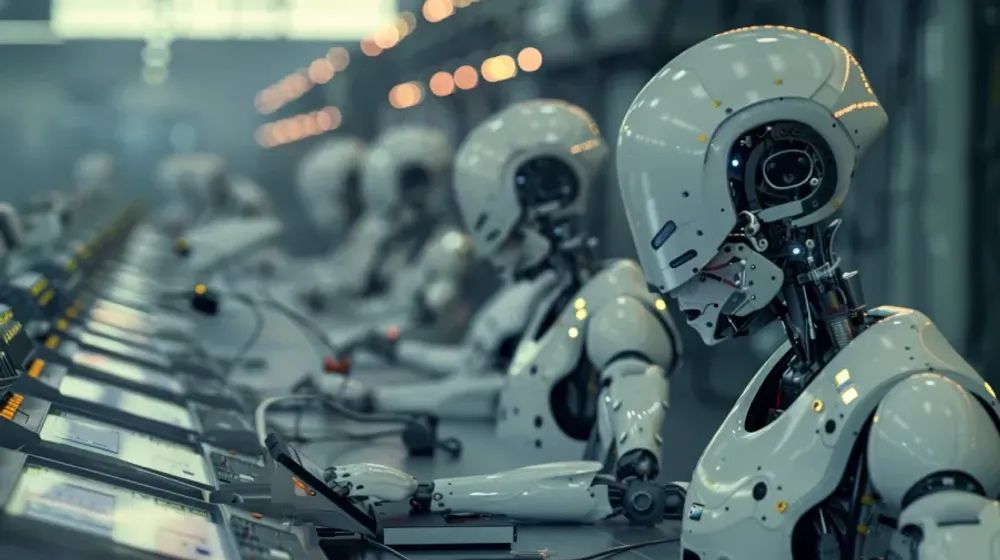
It’s been four years since I started this blog with a simple but powerful idea: there’s massive potential for improvement in the operations of small and medium-sized factories. Today, I want to revisit this topic, especially in light of the incredible technological developments we’ve seen globally—yet, somewhat ironically, many of our factories still rely heavily on good old spreadsheets for their daily operations.
We’re in 2024, and while everyone’s buzzing about AI and its potential to revolutionize every industry, a surprising number of small and midsize manufacturing plants are still entrenched in the age-old practice of using spreadsheets for just about everything. From sales forecasting and order intake to production planning and resource allocation, these vital tasks are often managed in static, error-prone Excel files.
The Spreadsheet Saga Continues
In my day-to-day work, I’ve shifted more towards sales and product development, but my heart still lies with operations. Although we’ve incorporated some neat Python scripts here and there to automate data handling, it feels like we’re merely scratching the surface of what’s possible.
While tech enthusiasts are marveling at the rapid advancements in large language models (LLMs) and other cutting-edge technologies, our manufacturing facilities are often stuck trying to ensure that the right data gets to the right place without a hitch—a process that remains stubbornly manual.
The Potential of Tech Integration
Manufacturing is, undeniably, a critical part of our economy. Everything sold needs to be produced somewhere, and there’s an immense opportunity for growth if we can integrate more sophisticated technologies into these operations.
Imagine replacing those sprawling spreadsheets with dynamic, real-time systems that not only track but also predict and optimize manufacturing processes. The potential benefits are enormous, ranging from improved efficiency and reduced errors to enhanced ability to respond to market changes swiftly. You might be asking for some real-world examples of where technology can make a difference, and I can certainly share a few from my own experience:
- Automate CRM data entry: like it or not, sales department typically earns the most, so helping them to save time or close leads will be a guaranteed success.
- Enhancing quoting efficiency with any sort of database system, as providing a quote quickly puts you 50% closer to securing the order.
- Providing specialized tools for quoting high-margin items like spare parts to ensure competitive pricing and quick response times.
- Scraping data from PDFs; a task used plenty of times to save countless hours.
- Using advanced analytics for procurement and forecasting to improve order accuracy and reduce overstock.
- Integrating customer orders directly into manufacturing orders to reduce delays and errors, making the production cycle smoother.
- Implementing systems that alert for last-minute changes in customer orders to manage adjustments quickly and avoid costly delays.
- Optimizing logistics to calculate the best way to pack products into containers or trucks to maximize space and reduce shipping costs.
- Using image recognition to quickly spot defects in production without needing a quality inspector 24/7.
These examples illustrate just a slice of what’s possible when we apply modern technology to traditional manufacturing challenges, enhancing operational efficiency and overall business success. While the leap from spreadsheets to state-of-the-art tech might seem daunting, the transition can be gradual. Starting small—with one process or product line—can demonstrate the benefits of tech adoption and build momentum for wider implementation.
To my fellow engineers and software developers: there’s a world of opportunity in these factories. By focusing on solving one specific problem at a time, creating robust solutions, and iterating based on feedback, you can make a significant impact. I can’t stress enough how much these factories need your expertise.
Will these steps make you rich overnight? Most likely not. But remember, every bit of progress counts, and the cumulative effects of these improvements can become a huge asset in the future.