Image recognition in factories
- 19 May, 2024
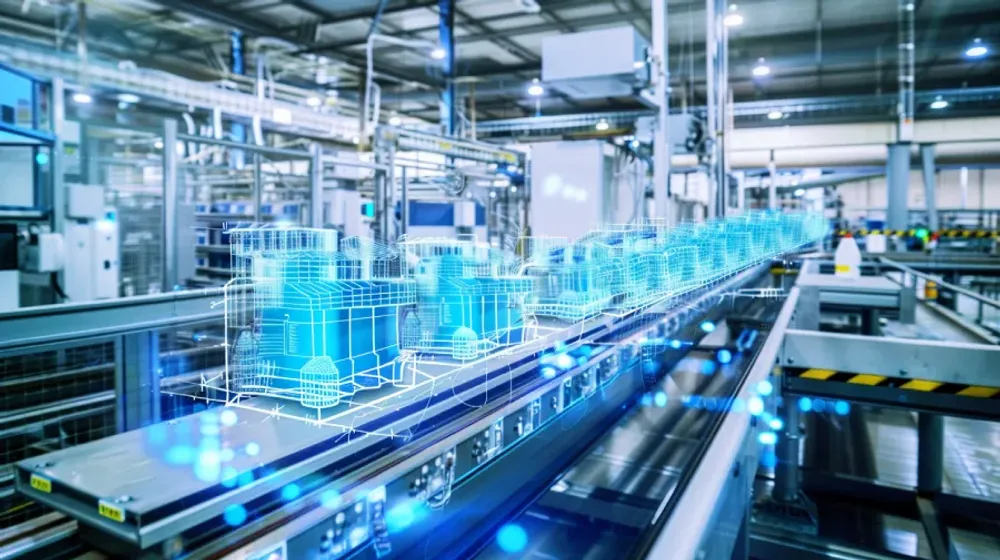
Today, I’d like to chat about something that’s been on my mind since I first stepped into the manufacturing world. Back then, the first thing I did was to make sure that every order leaving the factory was photographed. It wasn’t just about taking pictures though. We developed a quality checklist to match customer requirements with what was actually being delivered. Photos were our proof, our records.
Fast forward to today, and it’s heartening to see some factories embracing this approach. Capturing lots of photos has become a norm for some, and rightly so. But here’s a twist: simply taking a picture doesn’t guarantee that the component is correct. You could have an incorrect part, snap a photo, and off it goes. No one checks it. That’s where the problem lies. It’s like capturing a moment but missing the story.
This brings me to a fascinating aspect of technology that can revolutionize how we handle quality control: image recognition. Technologies like YOLO algorithms or convolutional neural networks could significantly enhance our ability to verify components at a glance. Training these systems can be a bit costly and complex, sure, but the benefits? They’re immense.
Imagine this scenario: a warehouse worker receives an order. Instead of manually checking each component, they scan it and let the pre-trained network do its magic. A photo is taken with a tablet, and instantly, the system confirms whether the component matches the order specifications. If there’s a mismatch, it alerts the operator before the product ever leaves the factory floor.
The beauty of this setup isn’t just in catching errors. It’s about moving from reactive to proactive measures. Currently, if a wrong component reaches a client, it’s a reactive action to address the claim. But with automated image recognition, we’re preventing the error right at the start. That’s a game changer.
Let’s not underestimate the cost savings either. Reducing manual checks means we can allocate resources more efficiently, perhaps even reducing the need for extensive manual labor over something as simple as verifying colors or shapes.
Futuristic Technology & Happy Customers
Moreover, consider the customer experience. When clients know that every component they receive has passed through a rigorous, automated quality check, their trust in the product—and in us—increases. This isn’t just about saving time or money; it’s about building a reputation as a reliable supplier.
Imagine integrating this technology into factory tours. Showing prospective clients and partners that our system autonomously weeds out defects can provide a substantial boost to our credibility and sales. It’s the kind of return on investment that doesn’t just save money but also secures new business through enhanced trust and reliability.
So, why isn’t everyone doing this? Well, implementing such a system can be daunting. The cost of training, the complexity of integration, and the time it takes to launch can be significant. However, for standard projects with standard components, the benefits far outweigh these initial hurdles.
I’ve seen firsthand the potential of what these technologies can offer, and I believe it’s only a matter of time before this becomes the new norm. It’s not just about adopting new technologies for the sake of innovation. It’s about practical, impactful changes that enhance the way we work and the quality we deliver.
In conclusion, while the leap to image recognition in manufacturing might seem like a giant step, it’s one that can fundamentally shift our approach to quality control. It’s about ensuring that every component, no matter how small, is correct. It’s about giving ourselves and our customers the peace of mind that comes with knowing that what we produce isn’t just good—it’s perfect.