Forecasting in factories
- 23 Dec, 2021
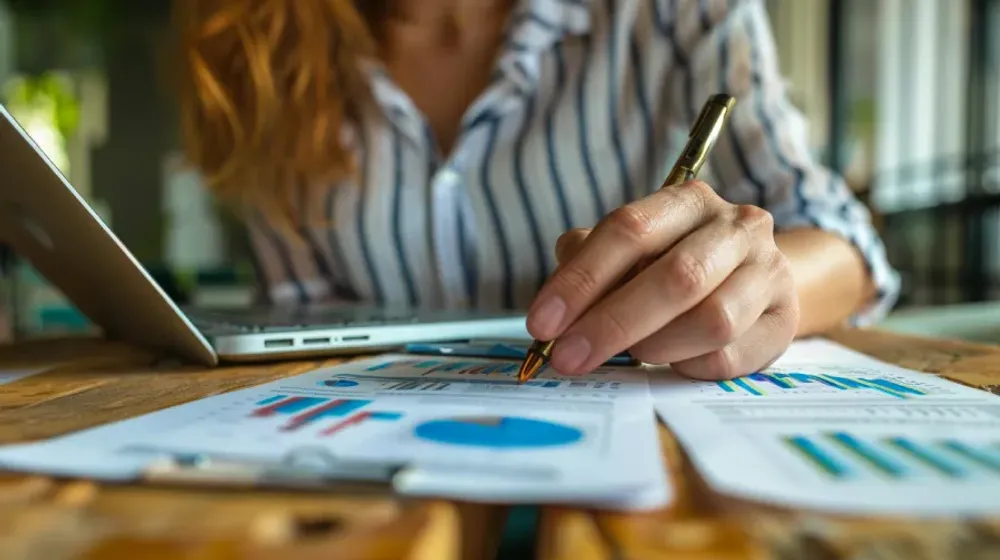
In today’s fast-paced business world, it’s surprising how many factories still operate without any form of statistical forecasting. Instead of leveraging advanced techniques to predict future demand, many purchasing departments rely on rudimentary methods that barely scratch the surface. This approach not only limits growth but also misses out on significant opportunities for profitability and efficiency.
Most factory data comes in the form of tables—rows and columns filled with numbers and dates. This kind of tabular data is the most typical in the business world. Yet, despite its potential, it’s often underutilized. Imagine the profits that could be reaped if machine learning techniques were applied to this data. Companies could optimize their supply chains, reduce waste, and improve customer satisfaction. For the indie hackers who develop these systems, the rewards could be substantial as well.
The Lack of Data-Driven Workers
In many factories, the workforce consists mainly of mechanical, electrical, or civil engineers, along with finance and marketing departments. But what’s often missing are data engineers—professionals who can harness the power of data to drive decisions. Without these experts, factories typically resort to outdated methods: someone checks last year’s demand for a few critical components (usually following the 80/20 rule), and that’s it. Rarely is there a dedicated person to set safety stock, reorder points, and order quantities, let alone apply sophisticated forecasting techniques.
Even simple statistical methods can make a big difference. Techniques like ARIMA (AutoRegressive Integrated Moving Average) or simple moving averages can help factories anticipate demand more accurately.
- Simple Moving Averages: This technique smooths out short-term fluctuations and highlights longer-term trends or cycles. It’s easy to implement and can provide quick insights into future demand.
- ARIMA: This method is useful for understanding and predicting future points in a series. It’s particularly good for data with trends and seasonality, making it ideal for forecasting demand for products that have predictable cycles.
Consider a factory that produces HVAC equipment. Heating products are typically sold during autumn and winter, not during summer. By applying seasonal adjustments to the forecasting model, the factory can better prepare for demand spikes and avoid overproduction during off-peak seasons.
Advanced Forecasting Techniques
While traditional methods are a good start, more advanced techniques can provide even better results. Tree models, LightGBM, and XGBoost are powerful tools that can handle complex patterns in data.
- Tree Models: These models split the data into different branches to make predictions. They are easy to understand and interpret, making them a good choice for those new to machine learning.
- LightGBM and XGBoost: These are advanced implementations of gradient boosting algorithms. They work by building an ensemble of trees, where each tree corrects the errors of the previous one. This method is particularly robust and can handle large datasets with high accuracy.
Gradient boosting algorithms, like LightGBM and XGBoost, are designed to optimize predictions by focusing on the hardest-to-predict cases. Here’s a simple explanation:
- Initial Model: Start with a simple model that makes basic predictions.
- Error Calculation: Calculate the errors of the initial model. This is the most forgotten part of all the forecasting techniques.
- New Model: Build a new model that focuses on correcting the errors of the initial model.
- Combine Models: Combine the initial and new models to improve overall predictions.
- Repeat: Repeat the process, each time focusing on the remaining errors.
This iterative approach ensures that the model becomes more accurate over time. For a factory, this means better predictions of future demand, optimized inventory levels, and improved customer satisfaction.
The Cost of Ignoring Forecasting
Not using any forecasting techniques can significantly impact a company’s bottom line. Customers are usually willing to pay more for quick availability. If your factory can meet lead times that match customer expectations, you’re more likely to win projects. This was evident in 2020/2021 when factories with good inventory management thrived despite the global chip shortage caused by COVID-related shutdowns.
On the flip side, having too much stock can be just as detrimental. With rising interest rates, holding excess inventory can be costly. You pay more for storage, and your capital is tied up in unsold products. Efficient forecasting can help maintain a balance—ensuring that you have enough stock to meet demand without overburdening your finances.
Forecasting isn’t just about crunching numbers; it’s an art. It requires a mix of traditional and modern techniques, a deep understanding of your market, and a willingness to adapt. For the modern business owner, embracing statistical and machine learning methods for forecasting can lead to better decision-making, higher profits, and a competitive edge in the market. So, take the leap—invest in data-driven workers, explore advanced forecasting models, and transform your factory’s approach to inventory management. The future of your business may depend on it.